The Product
PE60 is an innovative product covered by two patents, the result of three years of research, laboratory analysis, and industrial testing. It is a granular composite material created by agglomerating two components: biocarbon and recycled plastic obtained from the mechanical processing of PolyAl.
Designed for use in electric arc furnaces that recycle ferrous scrap, PE60 is intended to be the most sustainable foaming and reducing agent in the world. It defines an innovative approach where seemingly distant industrial supply chains integrate to solve their respective challenges and to provide future generations with a better future.
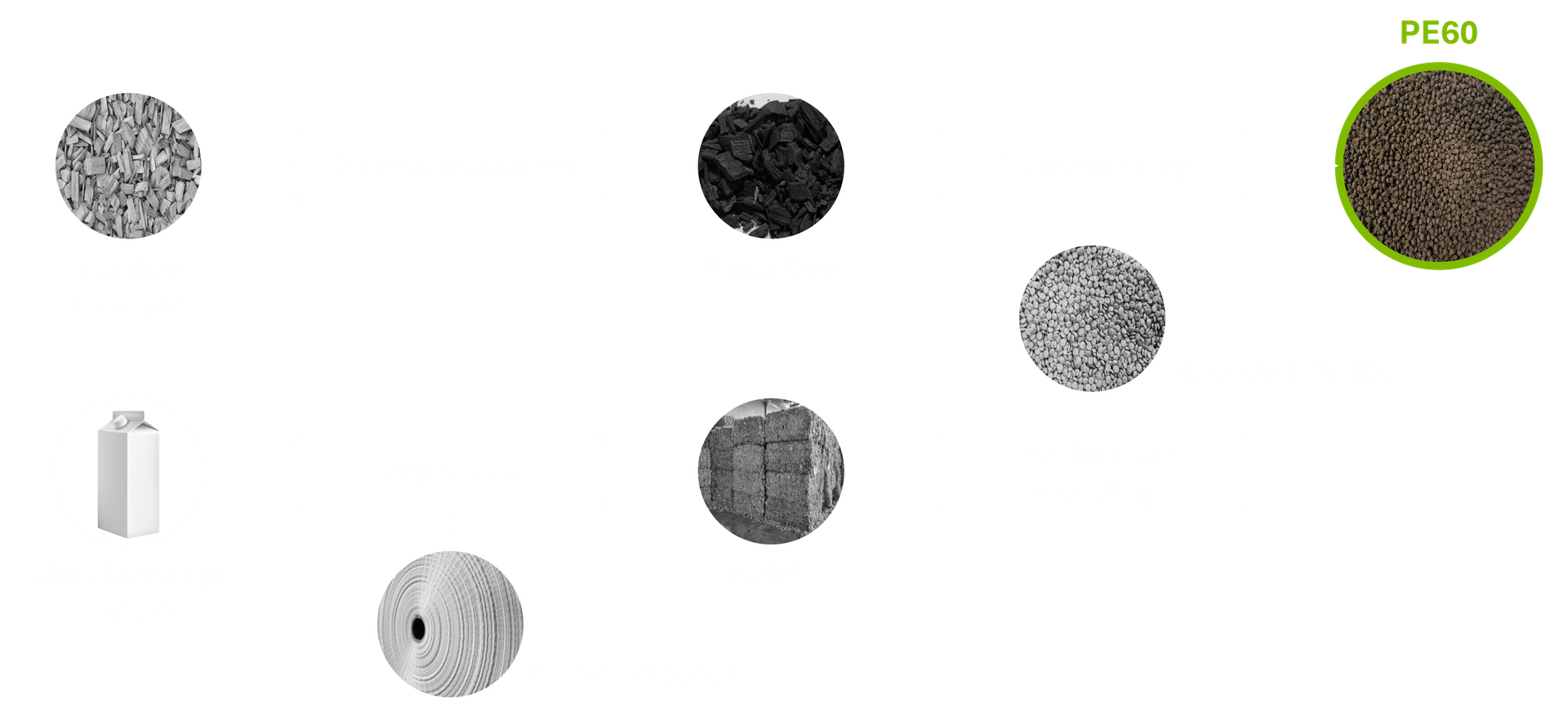

Biocarbon
Biocarbon is a renewable material obtained from sustainably sourced biomass. Depending on the type of biomass used and its treatment, biocarbon acquires specific chemical properties, making it a material of great interest for various applications. For decades, researchers and the steel industry have been exploring ways to use biocarbon as a substitute for fossil coal injected into electric arc furnaces. However, these efforts have faced several critical challenges associated with biocarbon:
- Safety
- Difficulties in handling and processing
- Injection challenges
- Limited chemical reactivity with slag
The technology behind PE60 was developed to overcome all these challenges, enabling the safe and efficient use of biocarbon.
A renewable material
Biocarbon is a renewable and climate-neutral resource, as it is derived from sustainably sourced biomass. The use of residual biomass creates synergistic integrations between diverse sectors, enhancing the positive environmental impact of biocarbon.
Creating value
Thanks to PE60, biomass that is currently used as fuel can now be repurposed as a raw material. Residues such as sawdust from wood processing or forest maintenance byproducts can be diverted from energy use and instead be valued for their unique characteristics: biomass is the only source of renewable carbon available to humanity.
Endless possibilities
Depending on the type of biomass used and the thermal treatment applied, biocarbon acquires various chemical properties. With PE60, any type of biocarbon can be used quickly and easily, with its characteristics tailored to the desired reaction mechanisms within the steelmaking process. Additionally, different types of biocarbon can be blended within PE60 to create the ideal product.
Recycled Plastic and PolyAl
Beverage cartons (also known as tetrapak) are among the most widely used packaging materials globally. Their unique and ingenious structure allows for optimal distribution and preservation of perishable liquids such as milk, fruit juices, and sauces. These multi-layered materials consist of paper, plastic, and aluminum.
When beverage cartons are collected for recycling, they are separated and sent to specialized paper mills that recover the paper fraction to transform it into new products. The remaining plastic and aluminum fraction is concentrated into a waste material called PolyAl, which is currently primarily destined for energy recovery or landfill.
PolyAl can be mechanically processed to produce high-quality recycled plastic, suitable for a stable and effective agglomeration process with biocarbon.
Due to its chemical and physical properties, recycled plastic derived from PolyAl is the ideal polymeric material for the production of PE60.

A global model
Steel mills that recycle ferrous scrap exist worldwide and are expected to multiply in the coming decades. By generating a consistent and steady demand for PE60, these steel mills can incentivize paper mills to process beverage cartons, thereby boosting the entire recycling supply chain, particularly in regions where such packaging is not yet being recycled.
To date, 73% of beverage cartons (3.5 million tons per year) are not recycled.
At a European level, the goal of beverage carton manufacturers is to recycle over 500,000 tons of paper and 250,000 tons of PolyAl annually by 2030.
Valuable aluminum
Due to its exceptional affinity for oxygen, aluminum is used in steel mills that recycle ferrous scrap for both environmental and metallurgical functions. Approximately 10% by weight of the recycled plastic from PolyAl consists of aluminum. Thus, recycling PolyAl and using PE60 enables the recovery of this valuable metal that would otherwise be wasted.
Renewable plastics
Beverage cartons are seeing ever-increasing renewable plastic content. In 2023, 8% of the plastic used by the main producer is of biogenic origin, having placed on the market 10.4 billion packages and 12.6 billion caps made with plant-based plastics (a growth compared to 2022 of 18% and 6% respectively). The plant-based plastic is therefore added to the content of renewable and climate-neutral materials present in PE60, leading to a product whose CO2 emissions are going to reduce over time with the evolution of beverage cartons.
PE60: A Product for the Future
Through an advanced agglomeration process, PE60 is produced as a technical compound with unique characteristics:
DECARBONIZATION
RENEWABLE MATERIALS
QUALITY
CLEAN
CIRCULARITY
SYNERGIES

Continuous collaboration with steel mills
Pipex Energy closely collaborates with steel mills to develop customized PE60 formulations for each production site. This engineering process is focused on defining the chemical-physical properties of materials that best fit the furnace type, the steel grades produced, the practices adopted, and the injection systems in place. This approach optimizes the performance of PE60, maximizing its environmental benefits.